
20T/h sawdust pellet production line
Category:
Pellet Line
Chat with us now for a quick response.
Get expert sales advice within 12 hours.
Keyword:
20T/h sawdust pellet production line
Product introduction
This sawdust pellet production line consisits of 7 sets JS700 wood pellet machine, with max output of 15-17t/h.
The production process include: wood chipping, crushing, drying and pellet making.
We can make a proposal for you according to your real situation.
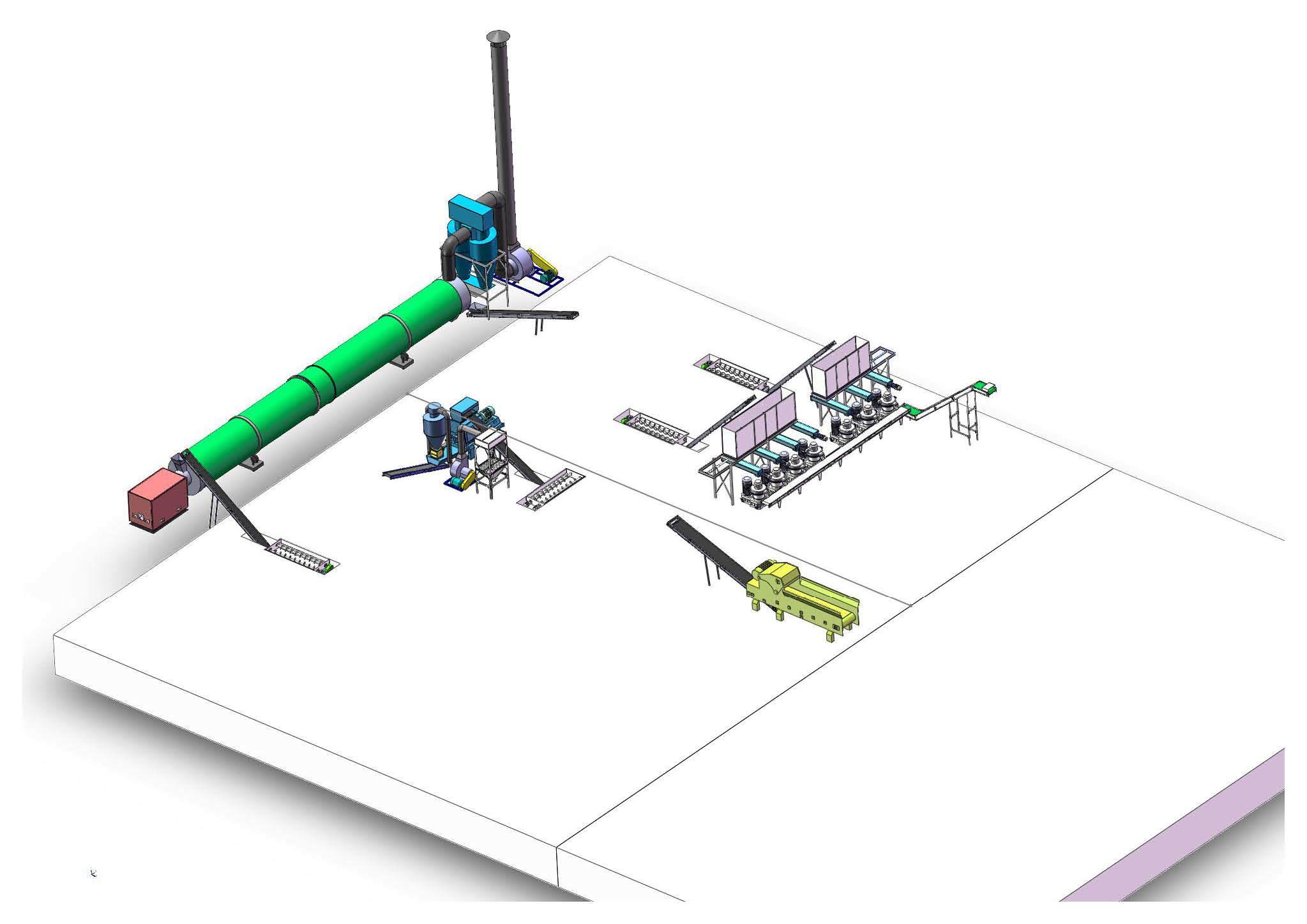
20T/h Sawdust Pellet Production Line
In the field of biomass energy utilization, the 20T/h sawdust pellet production line plays a significant role.
I. Introduction
Sawdust, as a common biomass material, has great potential for conversion into high - quality pellets. A 20T/h sawdust pellet production line is designed to handle a relatively large amount of sawdust and transform it into pellets efficiently.
II. Components of the Production Line
Raw Material Pretreatment System
The sawdust needs to be properly pretreated before pelletization. This may include drying to reduce the moisture content. If the moisture content is too high, it will affect the quality of the pellets. For a 20T/h production line, a powerful drying unit is required to ensure that the sawdust reaches the optimal moisture level, usually around 10 - 15%.
Screening is also an important part of pretreatment. It helps to remove impurities such as large pieces of wood, stones, and metal fragments that may be mixed with the sawdust.
Pelletizing Machine
The pelletizing machine is the core of the production line. It uses mechanical pressure to compress the sawdust into pellets. For a 20T/h production line, the pelletizing machine should have a high - capacity die and roller system. The die is typically made of high - quality alloy steel, which can withstand high pressure and continuous operation. The rollers rotate and press the sawdust into the holes of the die, forming pellets of a specific shape and size.
Cooling System
After the pellets are formed, they are hot and need to be cooled. A cooling system, usually consisting of a cooler with a large - capacity fan, is used to quickly reduce the temperature of the pellets. This not only helps to solidify the pellets but also improves their quality and durability.
Packaging System
The final step in the production line is packaging. Given the high - output rate of 20T/h, an automated packaging system is essential. This system can weigh the pellets accurately and package them into bags or containers of different sizes, ready for transportation and storage.
III. Advantages of the 20T/h Sawdust Pellet Production Line
High Efficiency
With a production capacity of 20T/h, it can meet the large - scale production needs of biomass pellets. This is especially important for industries that require a large amount of pellet fuel, such as power plants and heating companies.
Quality Assurance
Through precise control of each production process, the quality of the pellets can be well - guaranteed. The pellets produced are uniform in size, high in density, and have good combustion performance.
Environmental Benefits
By converting sawdust into pellets, it effectively utilizes biomass resources, reducing waste and environmental pollution. The use of sawdust pellets as an alternative fuel can also reduce the dependence on fossil fuels, contributing to the reduction of greenhouse gas emissions.
IV. Conclusion
The 20T/h sawdust pellet production line is a crucial piece of equipment in the biomass energy industry. It combines high - efficiency production, quality control, and environmental protection. With the continuous development of biomass energy technology, such production lines are expected to play an even more important role in the future, promoting the sustainable use of biomass resources and the development of clean energy.
The biomass pellet production line is a comprehensive production system that processes biomass raw materials into pellet fuels. It usually includes the following main steps: raw material collection and crushing, drying, granulation, cooling, and packaging.
Biomass pellet production lines can be classified by the type of raw materials.
Wood based biomass pellet production line: The main raw materials include sawdust, wood chips, wood powder, waste wood, etc., suitable for wood waste generated by wood processing plants, furniture factories, etc.
Straw based biomass pellet production line: The main raw materials are agricultural waste such as corn straw, wheat straw, and rice straw, which are suitable for agricultural planting areas.
Other biomass pellet production lines: using peanut shells, edible mushroom residue, urban greening waste, etc., have great development potential.
A modern pellet production line adopts advanced integrated technologies, and has a high degree of automation, high production efficiency, and stable product quality.
A complete biomass pellet production line usually includes the following sections and corresponding equipment:
Chipping section: Crushing large raw materials into small pieces.
Crushing section: further pulverize the crushed raw materials into fine powder.
Drying section: Dry the fine powder to the appropriate moisture content.
Granulation section: Press the dried fine powder into pellet fuel.
Cooling section: Cool the produced pellet fuel to room temperature.
Packaging section: Packaging the cooled pellet fuel.
Biomass pellet production lines are widely used in the processing of various biomass raw materials, such as waste from wood processing plants, agricultural waste, etc. Its advantages include:
Energy conservation and emission reduction: converting waste biomass resources into clean energy to reduce environmental pollution.
Reduce costs: Utilize waste as raw materials to lower production costs.
Improve energy utilization efficiency: The biomass pellet fuel produced has high calorific value, good combustion performance, and is suitable for use in various combustion equipment.
PRODUCT APPLICATION
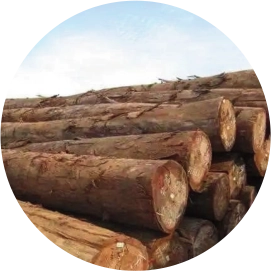
Straw
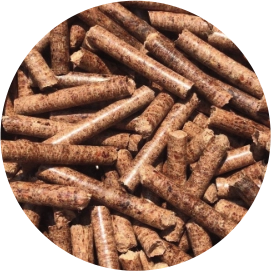
Straw pellet
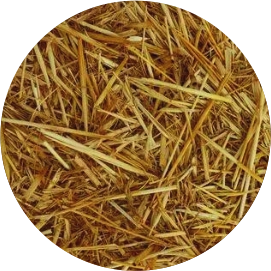
Sawduat
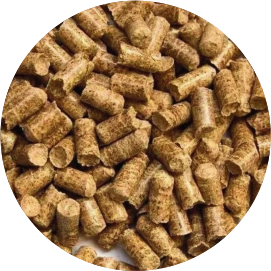
Sawduat pellet
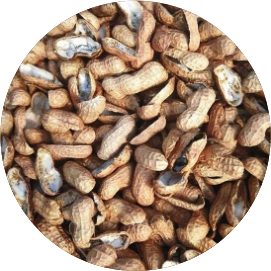
Peanut shell
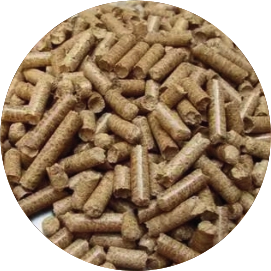
Nutshell pellet
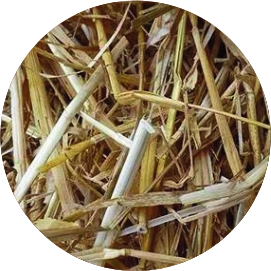
Straw
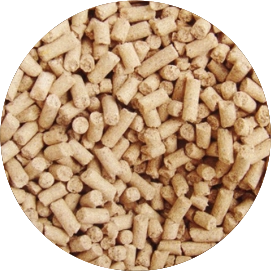
Straw pellet
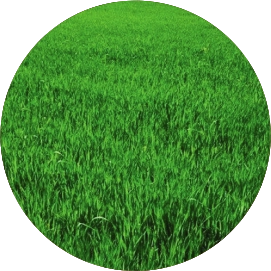
Grass
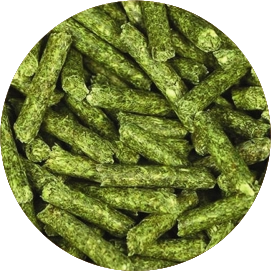
Grass pellet
Complete production line flow chart
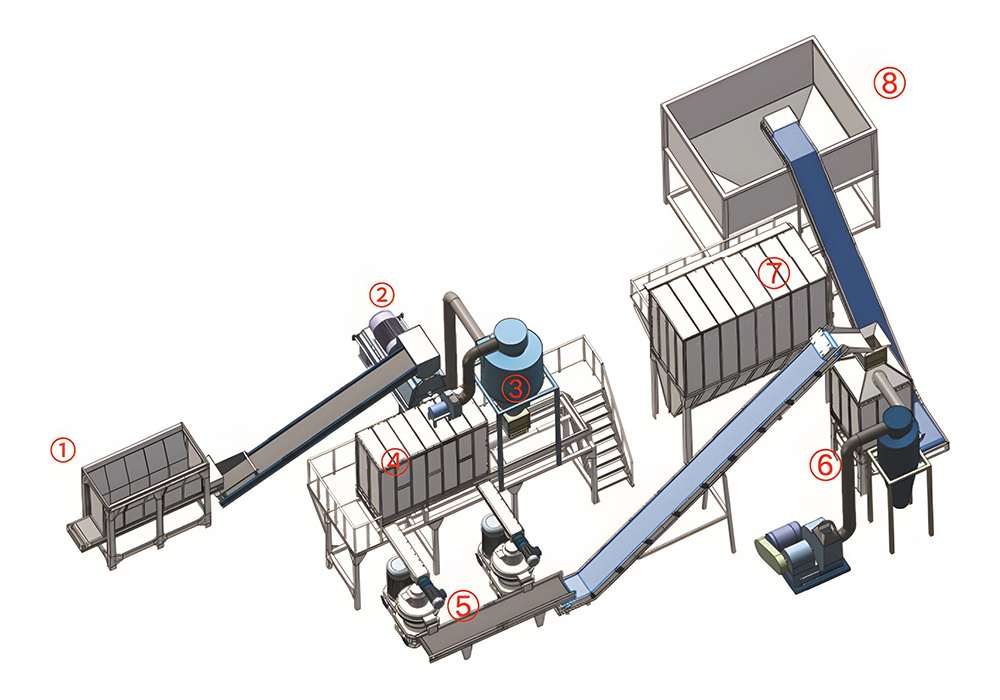
① Double twisted roller silo
② Crusher
③ Shakron discharge
④ Hydraulic silo
⑤ Particle machine
⑥ Cooling machine
⑦ Pulse dust removal
⑧ Finished product silo
Factory description

Shipping Packaging

Customer communication

CUSTOMER VISIT

CUSTOMER CASE
FAQ
RELATED PRODUCTS
SERVICE SUPPORT
Guide customers to select suitable device models
According to the special requirements of customers, design and manufacture products to solve related technical problems for customers
A full set of equipment warranty for one year (except for damaged parts)
GET A FREE QUOTE